Solutions for All Sizes
RFID Improves Inventory Visibility for Family-Owned Ibiley UniformsSummary
Industry: School uniform manufacturing, retail sales and distribution
Solutions:
- RFID (Radio Frequency Identification) tags and labels
- Sensormatic Implementation
- RFID Source Tagging at the factory
Benefits:
- Reduced inventory time by at least 75%
- Saved substantial amounts of labor expenses
- Increased inventory accuracy to better serve customers
The Profile
Ibiley Uniforms has been providing high-quality uniforms to students, families and schools for over 50 years. They are the leading school uniform provider for the entire United States and serve more than 100,000 students and more than 400 public, private and charter schools across the country.
The Challenge
Ibiley Uniforms, a family-owned school uniform manufacturer based in Miami, Florida, knew that modernizing inventory control between their brick-and-mortar retail, online and warehouse locations could help optimize operations. Ibiley has been serving their community for over 50 years by providing high-quality uniforms to students, families and schools. They are the leading school uniform provider for the entire United States and serve more than 100,000 students across the country.
The seasonal nature of their industry creates a demanding six-week turnaround time in which orders need to be placed and delivered in time for the school season. In a retail landscape in which shoppers expect products to be in-stock, on shelves and online (and delivered faster than before) gaining supply chain visibility to capitalize on this annual opportunity is key.
“If your inventory isn’t correct, you can’t service your customers” said Ibiley co-founder Eddy Barea. “The level of time and labor we were investing to complete our daily cycle counts was too much, delaying purchasing and product replacement at a time when shoppers were expecting orders to be filled faster.”
Ibiley knew that RFID technology, together with the implementation experts at Sensormatic Solutions and reseller POSDATA, could help them achieve the inventory accuracy needed to meet and exceed their customers’ expectations.
The Solution
Traditional inventory counting methods are known to be cumbersome and labor-intensive. Relying on manual methods requires time and labor that could be redirected to higher value areas like sales and customer assistance. As a growing business operating on a compressed time schedule, Ibiley was ready to adapt and advance its processes to maintain their edge as a national market leader.
The Sensormatic and POSDATA teams started by providing guidance on the right RFID solutions for Ibiley’s operations. With Sensormatic’s TrueVUE Cloud software in place, security tags and labels compatible with RFID were attached to each product in the uniform distributor’s inventory. Ibiley started Source Tagging with RFID labels from the factory and enabled exception RFID tagging at the distribution center in Miami with RFID printers. Ibiley was then able to cycle count at each of the locations, including the warehouse. RFID inventory counts are 26 times faster than barcode scanning because the technology only requires line of sight to work successfully. Ibiley now has accurate item-level inventory data in each location that matches their ERP system.
“After just two years, we’re already seeing ROI,” said Barea. “The new system allows us to scan products as they arrive and compare them instantly against the packing slips. After factoring in what we’re now saving on time and labor, it’s been a worthwhile investment.”
The Results
Ibiley improved their inventory accuracy which helped them unlock valuable item-level visibility throughout their supply chain.
With products equipped with RFID technology, they can complete inventory counting quickly and digitally, allowing for seamless updates to be made across retail, warehouse and online systems. Key highlights of the engagement included:
- Reducing inventory counting from one week to just a few hours
- Saving between $50,000 and $60,000 dollars in labor
- Improving ability to fulfill orders accurately and on time — each of which is vital for shopper experience, customer satisfaction, and business continuity
“The Sensormatic team was great to work with” Barea concluded. “They guided us through the entire process, and really helped us understand the benefits of all the software, equipment, and best practices involved in bringing the implementation to life.”
Having witnessed the many benefits afforded by RFID, Ibiley looks forward to future projects with the Sensormatic team and provided new ideas for their roadmap such as built in integrations to ERP systems, identifying unique items with special configurations and self checkout features. Like many retailers, they’ve realized that inventory visibility is just the beginning of what RFID can do for their operations. Umesh Cooduvalli, Sensormatic Business Development Executive said "RFID technology is not only beneficial for large global retailers, but also for smaller regional retailers with less than 10 stores...deployment can be quicker in these instances too" It’s a versatile solution, capable of helping retailers of all sizes improve inventory visibility and control to align with new demands from a changing retail landscape.
Ready to discover how Sensormatic Solutions can help you improve inventory visibility and accuracy through RFID? Contact one of our solutions experts today to find out how.
About Johnson Controls
At Johnson Controls (NYSE:JCI), we transform the environments where people live, work, learn and play. As the global leader in smart, healthy and sustainable buildings, our mission is to reimagine the performance of buildings to serve people, places and the planet.
Building on a proud history of nearly 140 years of innovation, we deliver the blueprint of the future for industries such as healthcare, schools, data centres, airports, stadiums, manufacturing and beyond through OpenBlue, our comprehensive digital offering.
Today, with a global team of 100,000 experts in more than 150 countries, Johnson Controls offers the world`s largest portfolio of building technology and software as well as service solutions from some of the most trusted names in the industry.
Visit www.johnsoncontrols.com for more information and follow @johnsoncontrols on social platforms.
About Sensormatic Solutions
Sensormatic Solutions is the leading global retail solutions portfolio of Johnson Controls powering operational excellence at scale and enabling smart and connected shopper engagement. Our intelligent digital operating platform – Sensormatic IQ – combines the full Sensormatic Solutions portfolio, including third-party data to deliver unmatched insights into shopper experience, inventory intelligence, loss prevention and operational effectiveness with advanced technologies, like AI and Machine Learning. This enables retailers to act on prescriptive and predictive data-driven outcomes to confidently move into the future. Please visit Sensormatic Solutions or follow us on LinkedIn, X, and our YouTube channel.
About POSDATA
POSDATA is a leader in the design, integration and implementation of mobile data collection, supply chain management, and loss prevention systems for the retail industry. We have been providing innovative technologies to retailers for over 50 years. POSDATA has partnered with Sensormatic to deliver the latest technologies in shopper analytics, loss prevention and RFID-based inventory management solutions to maintain extremely accurate inventories as needed in today’s multi-channel retail environments. Visit us at www.posdata.com.
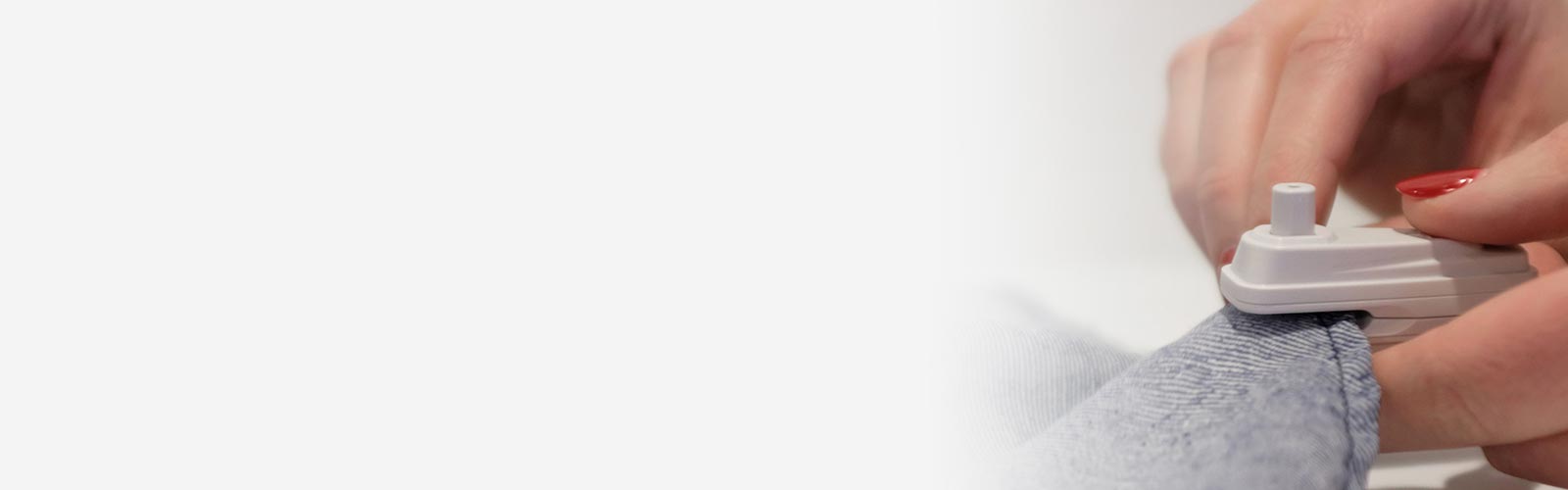